Maszyny pneumatyczne to urządzenia, które wykorzystują sprężone powietrze do wykonywania różnorodnych prac. Kluczowymi elementami ich budowy są kompresory, zbiorniki powietrza, zawory oraz siłowniki pneumatyczne. Kompresory odpowiadają za sprężanie powietrza, które następnie jest magazynowane w zbiornikach. Zbiorniki te muszą być odpowiednio zaprojektowane, aby wytrzymać wysokie ciśnienie, co zapewnia ich trwałość i bezpieczeństwo użytkowania. Zawory natomiast kontrolują przepływ powietrza w systemie, umożliwiając precyzyjne sterowanie działaniem maszyny. Siłowniki pneumatyczne przekształcają energię sprężonego powietrza na ruch mechaniczny, co pozwala na wykonywanie różnych zadań, takich jak podnoszenie, przesuwanie czy formowanie materiałów. Warto również zwrócić uwagę na elementy dodatkowe, takie jak filtry i osuszacze powietrza, które zapewniają czystość i odpowiednią jakość sprężonego powietrza, co jest kluczowe dla prawidłowego funkcjonowania całego systemu.
Jakie są zalety i wady maszyn pneumatycznych
Maszyny pneumatyczne mają wiele zalet, które przyciągają uwagę inżynierów i przedsiębiorców. Przede wszystkim charakteryzują się dużą mocą przy stosunkowo niewielkich rozmiarach, co sprawia, że są idealne do zastosowań w ograniczonej przestrzeni. Ponadto ich działanie jest ciche i nie generuje dużych wibracji, co wpływa na komfort pracy w otoczeniu przemysłowym. Maszyny te są również łatwe w obsłudze i konserwacji, co przekłada się na niższe koszty eksploatacji. Jednakże istnieją także pewne wady związane z ich użytkowaniem. Do najważniejszych należy konieczność dostarczania sprężonego powietrza oraz związane z tym koszty energii elektrycznej potrzebnej do zasilania kompresorów. Dodatkowo, jeśli system nie jest odpowiednio zabezpieczony przed zanieczyszczeniami, może dojść do uszkodzeń komponentów maszyn. Warto również pamiętać o ryzyku związanym z wysokim ciśnieniem sprężonego powietrza, które może prowadzić do niebezpiecznych sytuacji w przypadku awarii lub błędów w obsłudze.
Jakie są zastosowania maszyn pneumatycznych w przemyśle
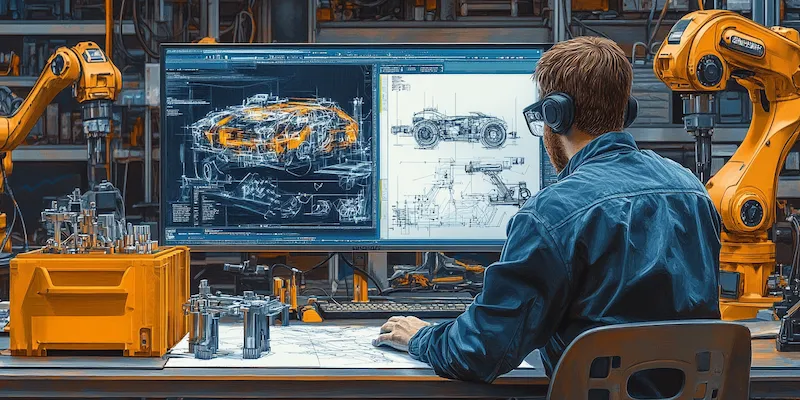
Maszyny pneumatyczne znajdują szerokie zastosowanie w różnych gałęziach przemysłu ze względu na swoją wszechstronność i efektywność. W przemyśle motoryzacyjnym używane są do montażu i demontażu części samochodowych oraz do malowania pojazdów za pomocą pistoletów natryskowych. W sektorze budowlanym maszyny te służą do podnoszenia ciężkich materiałów oraz do wykonywania prac wykończeniowych. W branży spożywczej wykorzystuje się je do pakowania produktów oraz transportu surowców przez systemy rur pneumatycznych. W przemyśle elektronicznym maszyny pneumatyczne odgrywają kluczową rolę w procesach montażowych oraz testowych komponentów elektronicznych. Również w logistyce maszyny te są wykorzystywane do automatyzacji procesów magazynowych oraz sortowania towarów. Dzięki swojej elastyczności maszyny pneumatyczne mogą być dostosowane do specyficznych potrzeb różnych branż, co czyni je niezwykle popularnym rozwiązaniem w nowoczesnym przemyśle.
Jakie są nowoczesne technologie w budowie maszyn pneumatycznych
W ostatnich latach nastąpił znaczący rozwój technologii związanych z budową maszyn pneumatycznych. Nowoczesne rozwiązania obejmują zastosowanie inteligentnych systemów sterowania, które pozwalają na precyzyjne zarządzanie procesami produkcyjnymi. Dzięki integracji z systemami automatyki przemysłowej możliwe jest monitorowanie parametrów pracy maszyn w czasie rzeczywistym oraz optymalizacja ich działania. Wprowadzenie technologii Internetu Rzeczy (IoT) umożliwia zdalne zarządzanie i diagnostykę urządzeń, co znacznie ułatwia konserwację i naprawy. Ponadto nowoczesne materiały używane do produkcji komponentów maszyn pneumatycznych przyczyniają się do zwiększenia ich trwałości oraz odporności na działanie wysokich ciśnień i temperatur. Wiele firm inwestuje również w rozwój ekologicznych rozwiązań, takich jak energooszczędne kompresory czy systemy recyklingu sprężonego powietrza. Te innowacje mają na celu nie tylko poprawę efektywności energetycznej maszyn, ale także zmniejszenie ich wpływu na środowisko naturalne.
Jakie są najczęstsze problemy z maszynami pneumatycznymi
Podczas eksploatacji maszyn pneumatycznych mogą wystąpić różnorodne problemy, które wpływają na ich wydajność i niezawodność. Jednym z najczęstszych kłopotów jest nieszczelność w układzie pneumatycznym, co prowadzi do utraty ciśnienia i obniżenia efektywności pracy maszyny. Nieszczelności mogą występować w różnych miejscach, takich jak połączenia rur, zawory czy uszczelki. Dlatego regularne przeglądy i konserwacja są kluczowe dla zapewnienia prawidłowego funkcjonowania systemu. Innym problemem są zanieczyszczenia sprężonego powietrza, które mogą prowadzić do uszkodzeń elementów roboczych, takich jak siłowniki czy zawory. Zastosowanie filtrów oraz osuszaczy powietrza jest niezbędne, aby zminimalizować ryzyko wystąpienia tego typu awarii. Warto również zwrócić uwagę na niewłaściwe ustawienia parametrów pracy maszyn, takie jak ciśnienie czy przepływ powietrza, które mogą prowadzić do nieefektywnego działania urządzeń.
Jakie są koszty eksploatacji maszyn pneumatycznych
Koszty eksploatacji maszyn pneumatycznych mogą być różnorodne i zależą od wielu czynników, takich jak rodzaj zastosowanej technologii, intensywność użytkowania oraz specyfika branży. Podstawowym kosztem jest energia elektryczna potrzebna do zasilania kompresorów, które sprężają powietrze. Koszty te mogą znacząco wzrosnąć w przypadku dużych zakładów przemysłowych, gdzie wymagane są wysokie przepływy powietrza. Dodatkowo należy uwzględnić koszty związane z konserwacją i serwisowaniem urządzeń, które są niezbędne dla zapewnienia ich prawidłowego funkcjonowania. Regularne przeglądy oraz wymiana zużytych komponentów mogą generować dodatkowe wydatki, ale są kluczowe dla uniknięcia poważniejszych awarii i długotrwałych przestojów. Warto również pamiętać o kosztach związanych z zakupem materiałów eksploatacyjnych, takich jak filtry czy oleje smarowe. Mimo że początkowe inwestycje w maszyny pneumatyczne mogą być wysokie, ich efektywność oraz możliwość automatyzacji procesów produkcyjnych często przekładają się na oszczędności w dłuższym okresie czasu.
Jakie są przyszłościowe kierunki rozwoju technologii pneumatycznych
Przemysł pneumatyczny stoi przed wieloma wyzwaniami związanymi z rosnącymi wymaganiami dotyczącymi efektywności energetycznej oraz ochrony środowiska. W związku z tym przyszłościowe kierunki rozwoju technologii pneumatycznych koncentrują się na innowacjach mających na celu zwiększenie wydajności i redukcję kosztów eksploatacji. Jednym z głównych trendów jest rozwój inteligentnych systemów zarządzania, które pozwalają na monitorowanie pracy maszyn w czasie rzeczywistym oraz optymalizację procesów produkcyjnych. Dzięki zastosowaniu sztucznej inteligencji możliwe będzie przewidywanie awarii oraz automatyczne dostosowywanie parametrów pracy maszyn do zmieniających się warunków. Kolejnym istotnym kierunkiem rozwoju jest poszukiwanie ekologicznych rozwiązań, takich jak energooszczędne kompresory czy systemy odzysku energii ze sprężonego powietrza. Wprowadzenie materiałów o lepszej trwałości i odporności na działanie wysokiego ciśnienia przyczyni się do zwiększenia żywotności komponentów maszyn pneumatycznych. Również rozwój technologii bezprzewodowych umożliwi łatwiejszą integrację systemów pneumatycznych z innymi rozwiązaniami automatyki przemysłowej.
Jakie są różnice między systemami pneumatycznymi a hydraulicznymi
Systemy pneumatyczne i hydrauliczne to dwa różne podejścia do przenoszenia energii mechanicznej w różnych aplikacjach przemysłowych. Główna różnica między nimi polega na medium roboczym – w systemach pneumatycznych wykorzystywane jest sprężone powietrze, podczas gdy w hydraulicznych stosuje się ciecz (najczęściej olej). Systemy pneumatyczne charakteryzują się mniejszą gęstością medium roboczego, co sprawia, że są lżejsze i bardziej elastyczne w zastosowaniach wymagających szybkich ruchów lub zmian kierunku pracy. Z drugiej strony systemy hydrauliczne oferują większą moc i precyzję w przenoszeniu dużych obciążeń, co czyni je idealnymi do zastosowań wymagających dużej siły, takich jak prasy czy maszyny budowlane. Kolejną istotną różnicą jest sposób działania – systemy pneumatyczne działają na zasadzie sprężania gazu, co wiąże się z koniecznością dostarczania sprężonego powietrza oraz jego odpowiedniego magazynowania. W przypadku hydrauliki kluczowe znaczenie ma odpowiednia jakość cieczy roboczej oraz jej filtracja w celu uniknięcia uszkodzeń komponentów układu.
Jakie są najnowsze trendy w projektowaniu maszyn pneumatycznych
W projektowaniu maszyn pneumatycznych można zaobserwować kilka istotnych trendów wynikających z postępu technologicznego oraz rosnących oczekiwań rynku. Jednym z nich jest coraz większy nacisk na automatyzację procesów produkcyjnych poprzez integrację maszyn pneumatycznych z systemami robotyzacji i sztucznej inteligencji. Dzięki temu możliwe jest osiągnięcie wyższej wydajności oraz precyzji działania urządzeń. Kolejnym ważnym trendem jest rozwój modułowych konstrukcji maszyn, które pozwalają na łatwe dostosowywanie urządzeń do zmieniających się potrzeb produkcyjnych oraz szybką wymianę komponentów w przypadku awarii. Projektanci coraz częściej zwracają uwagę na aspekty ergonomiczne oraz bezpieczeństwo użytkowników, co prowadzi do tworzenia bardziej przyjaznych dla operatora interfejsów oraz zabezpieczeń przed niebezpiecznymi sytuacjami związanymi z wysokim ciśnieniem sprężonego powietrza. Warto również zauważyć rosnącą popularność rozwiązań proekologicznych, takich jak energooszczędne kompresory czy technologie odzysku energii ze sprężonego powietrza.
Jakie są kluczowe czynniki wpływające na wybór maszyn pneumatycznych
Wybór odpowiednich maszyn pneumatycznych do konkretnego zastosowania powinien być oparty na kilku kluczowych czynnikach, które mają istotny wpływ na efektywność i niezawodność całego systemu. Przede wszystkim należy określić wymagania dotyczące mocy i wydajności urządzenia – to pozwoli na dobranie odpowiedniego typu kompresora oraz siłowników pneumatycznych do planowanych prac. Ważnym aspektem jest także analiza warunków pracy maszyny, takich jak temperatura otoczenia czy poziom wilgotności powietrza, które mogą wpływać na działanie układu pneumatycznego. Kolejnym czynnikiem jest dostępność serwisu oraz części zamiennych – wybierając producenta maszyn pneumatycznych warto zwrócić uwagę na jego renomę oraz wsparcie posprzedażowe oferowane klientom.